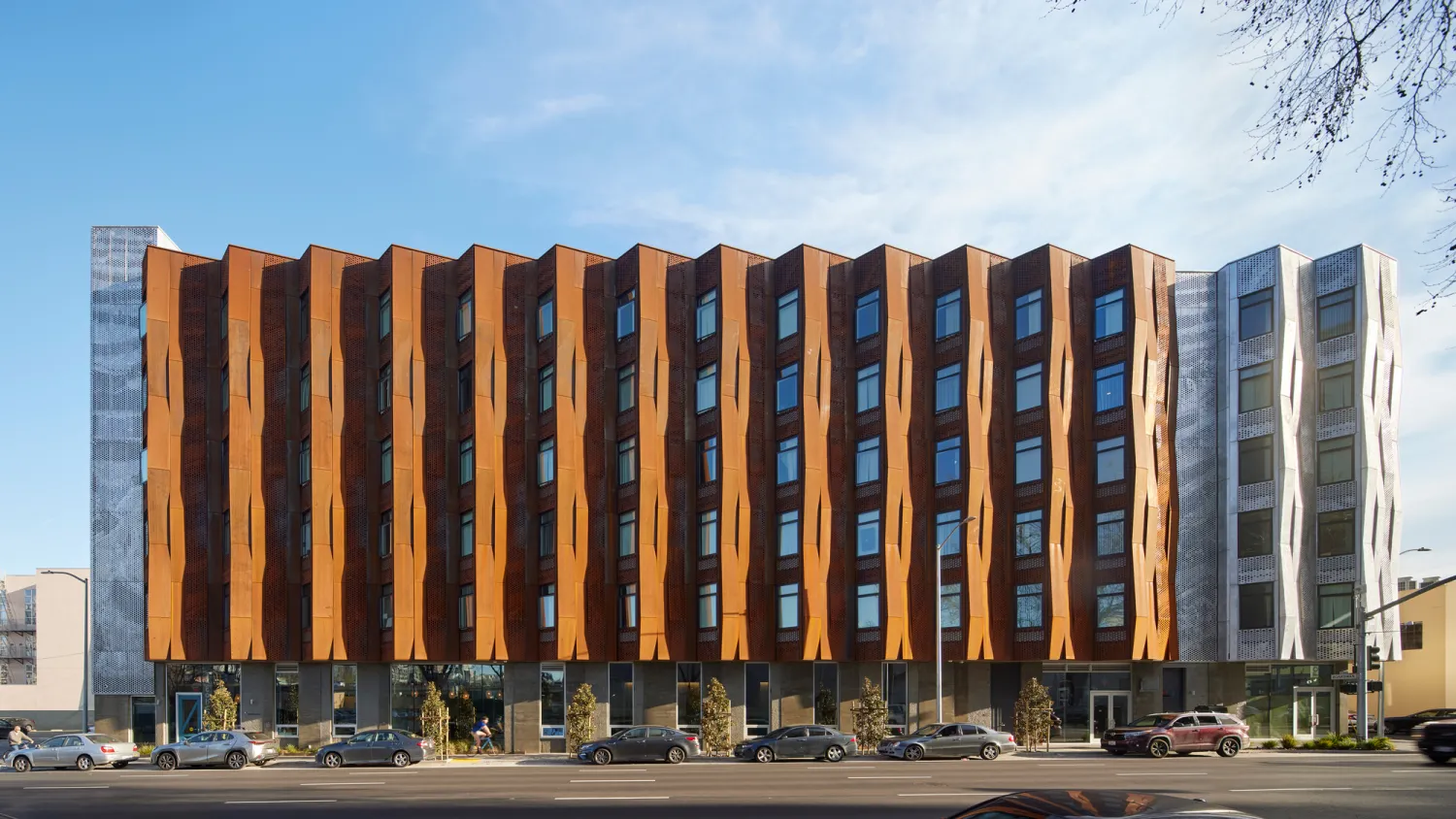
In response to San Francisco’s housing crisis, David Baker Architects (DBA) implemented a modular construction method and fast-tracked financing to deliver its Tahanan Supportive Housing complex. Located in the South of Market (SoMa) neighborhood, the project’s 63,000 square feet of space are distributed across six stories and provide 145 apartments for adults who have been homeless.
The effort’s funding came from a joint venture of Mercy Housing, Tipping Point Community, and the San Francisco Housing Accelerator Fund and the scheme was developed with the City’s Department of Homelessness and Supportive Housing. Utilizing the density bonus offered by California’s State Bill 35, which was passed to streamline housing construction, the project quickly received regulatory approval.
Constructed on an infill site, Tahanan includes a “community-focused” ground level space that includes access to a landscaped outdoor area, with the upper floors reserved for studio apartments. In approaching the building’s design, DBA wanted to honor the site’s location within the SOMA Pilipinas Cultural District. The name Tahanan “is a Tagalog word evoking the idea of ‘coming home’ and represents a place for people to return to or rest.” SOMA Pilipinas consulted the design team on further incorporating Philippine motifs into the project, with a pattern based on traditional handwoven mats cast into the project’s concrete, and a graphic of Philippine rice terraces depicted on the facade.
The facade was designed as a series of sawtooth-patterned bays sitting above a concrete podium, lining its main Bryant Street-facing facade. The units themselves were constructed from 87 mods that were installed on top of the poured-in-place concrete podium over ten days. As Weber explained, standard tolerances for wood-framed modular construction are 1/4 of an inch per ten feet of construction, and the installation process lends itself to imperfections.
Each module, manufactured by Factory OS, weighed between 20,000 and 30,000 pounds and was placed by cranes, with its final position manually adjusted within the constraints of the site using only hand tools. With this, imperfections can be visible on the facade, and adjusting them can tack-on costs and lengthen construction schedules.
This rainscreen design was fabricated from perforated steel with a rusted finish that helps with long-term durability and adds a material complexity to the facade. DBA associate and modular lead Jonas Weber told AN that the rainscreen was developed in close collaboration with BOK, and was “a design expression born out of a need to resolve a common challenge to modular projects.” As Weber explained, the main steel rainscreen, in addition to aluminum panels on other portions of the facade, “have integral mounting tabs which fasten directly to the exterior wall surface without the need for an additional furring system.” This design response allowed for the panels to “bridge” over marks of misalignment as each panel spanned ten feet.
The orientation of the sawtooth bays provides downtown views from the interiors, and hallways were oriented so that each end receives daylight. The facade is exposed to the sun facing northwest, while solar shading strategies were applied to the southeast-facing sections. Three-sided sunshades were installed into the rainscreen paneling on the building’s south-facing facade, and by tapering the siding panels’ returns additional penetrations were avoided through exterior waterproofing,” Weber told AN. The design team conducted solar heat gain studies to determine the depth of each sunshade. Solar photovoltaic panels on the roof help to offset building loads, further taking advantage of sunlight for energy performance.
DBA worked closely with BOK in developing the rainscreen during the design and construction process. DBA modeled the siding panels, sharing designs with BOK so that they could apply a tab and slot fastening system to allow DBA to review specific applications for Tahanan. The panels were ultimately tapered from two to eight inches in depth, creating more dynamic moments at corners and windows.
The resulting facade offers a sense of uniformity across its main front, with the silver-colored aluminum paneling bounding the shorter sides of the facade. This frames the rusted steel bays, “breaking the mass”, but not enough to create a sense of disjuncture. The panel arrangement also clearly delineates the ground floor podium, which was intended to be more public-facing. The installation method and attachment solutions made the fabrication process as efficient as possible.
Project Specifications
Architect: David Baker Architects
Location: San Francisco
Completion Date: November 2021
Developer: Mercy Housing California
Development Team: Tipping Point Community; San Francisco Housing Accelerator Fund
Structural Engineer: DCI Engineers
Civil Engineer: Luk + Associates
MEP Engineer: FARD Engineers
Landscape Architect: Fletcher Studio
General Contractor: Cahill Contractors
Modular Fabricator: Factory_OS
Custom Rainscreen: BOK Modern
Custom Furnishings: DBA_Workshop; Pacassa Studio
View the full article: David Baker Architects screens a modular, supportive housing project in San Francisco with weathered steel in The Architect's Newspaper.